Ethanol is available in several different blends for use in conventional and flexible fuel vehicles.
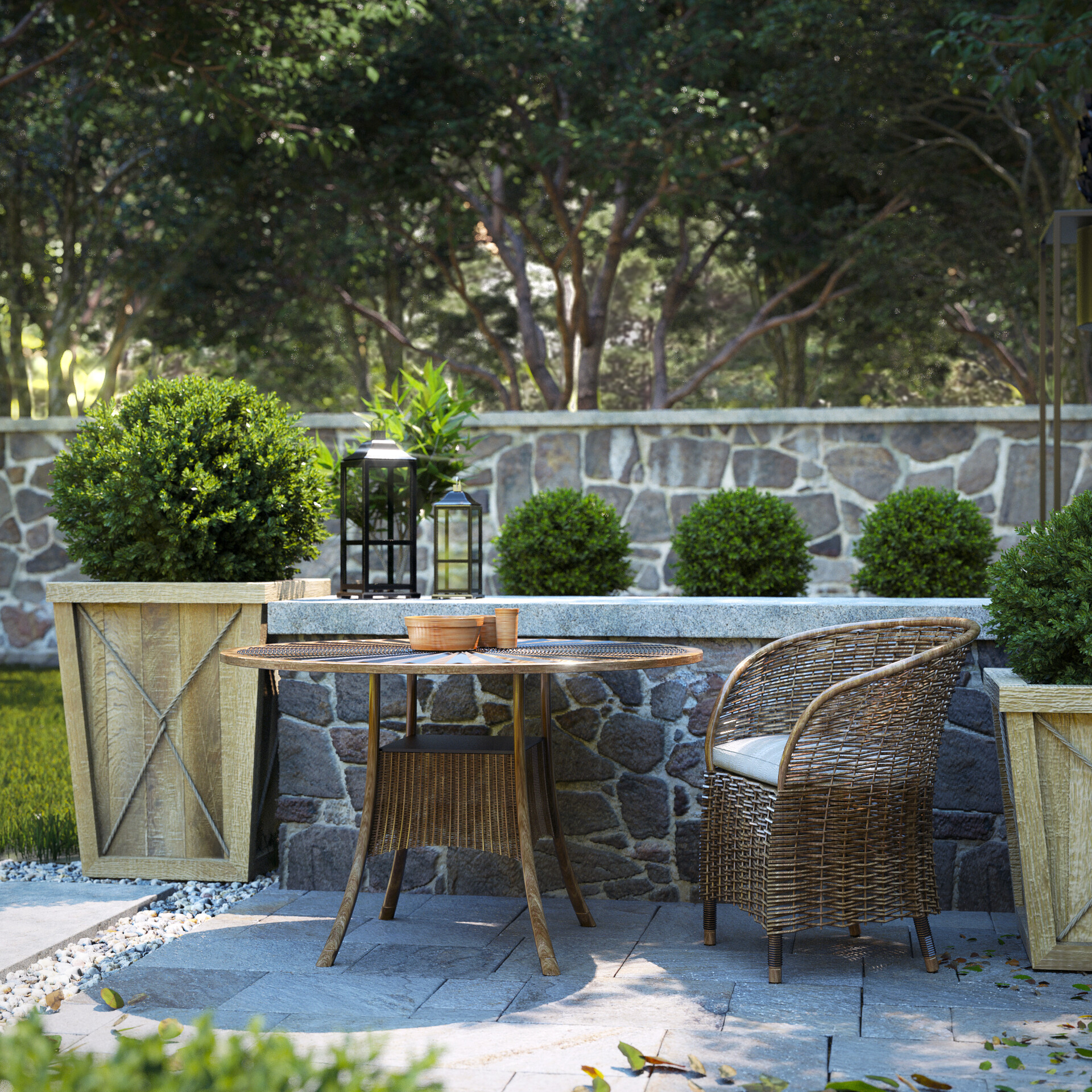
E10
Yes, there is an official Octane Blender. You are able to use up 20 GPUs (I believe that’s the current limit) with each license. Yes, I have always had Octane with all of features. Many of which I never need. AI Upsampler: Octane now includes a built-in AI up-sampler in Octane Imager. The AI up-sampler works similar to the AI denoiser first introduced in Octane 4, with a progressive and a one-stop up-sampling mode. You can now specify multiple sampling modes (2×2, 4×4) up-sampling for your rendered image directly in Octane. Get all of my add-ons, including AP Octane, at for Blender, how to install for free. Here's a link to the pla.
E10 is a low-level blend composed of 10% ethanol and 90% gasoline. It is approved by the U.S. Environmental Protection Agency (EPA) for use in any conventional, gasoline-powered vehicle. The use of E10 was spurred by the Clean Air Act Amendments of 1990 (and subsequent laws), which mandated the sale of oxygenated fuels in areas with unhealthy levels of carbon monoxide. This kicked off modern U.S. ethanol industry growth. Today, E10 is sold in every state. More than 98% of U.S. gasoline contains up to 10% ethanol to boost octane, meet air quality requirements, or satisfy the Renewable Fuel Standard. E10 does not qualify as an alternative fuel under the Energy Policy Act of 1992 (EPAct).
E15

E15 is a low-level blend composed of 10.5% to 15% ethanol and gasoline. E15 is approved for use in model year 2001 and newer light-duty conventional vehicles. Stations must adhere to several EPA requirements and regulations when selling E15. An important requirement is implementation of a misfueling mitigation plan to reduce the risk of vehicles older than model year 2001 refueling with E15. While E15 does not qualify as an alternative fuel under EPAct, it does help meet the federal Renewable Fuel Standard.
E85
E85 (or flex fuel) is an ethanol-gasoline blend containing 51% to 83% ethanol, depending on geography and season that qualifies as an alternative fuel under EPAct. E85 can be used in flexible fuel vehicles (FFVs), which have an internal combustion engine and are designed to run on E85, gasoline, or any blend of gasoline and ethanol up to 83%. FFVs have been produced since the 1990s, and more than 60 models are currently available. Since FFVs look just like gasoline-only models, visit Fueleconomy.gov to learn how to identify a flex-fuel vehicle or use the Alternative Fuel and Advanced Vehicle Search to find current FFV models. E85 is not approved for use in gasoline-only models.
Intermediate Blends from Blender Pumps
Blender pumps are dispensers that draw and blend fuel from two tanks. For example, a blender pump dispenser can offer three grades of gasoline (regular, premium, mid-grade) by storing regular and premium in two tanks underground. The dispenser is then able to blend the two to offer mid-grade gasoline. Ethanol blender pumps work the same way, with regular gasoline and E85 stored in two tanks. Intermediate blends are for use in FFVs and offer owners more options. Common blends, in addition to E85, include E25 (25% ethanol, 75% gasoline) and E30 (30% ethanol, 70% gasoline). Labels must clearly indicate blender pump fuels for FFVs. Blender pumps are also a legal method to dispense E15 to conventional vehicles, model year 2001 and newer.
High-Octane Fuel
The U.S. Department of Energy’s (DOE) Bioenergy Technologies Office funded a project to assess the potential of high-octane fuel (HOF) to reduce energy consumption and greenhouse gas emissions, as well as to understand barriers to its successful market introduction. The project focused on HOF with an ethanol content of 25% to 40% for use in a vehicle engine specifically designed to take advantage of the high octane content of the fuel. Industry continues to investigate the potential of high-octane ethanol fuel. Additional details of the HOF study and publications are available on the Bioenergy Knowledge Discovery Framework.
The Co-Optimization of Fuels & Engines (Co-Optima) initiative is an ongoing DOE-funded multi-national laboratory program evaluating high-octane fuels, including ethanol, to improve vehicle efficiency.
Similar to many other areas in refinery optimization, people can fool themselves into believing that operations are well when they are not. In this article, I will explore the common mistakes that refineries make when trying to minimize gasoline octane giveaway.
Often times, refinery blenders are not engineers, but rather operators that have made their way up the ranks. These folks are very intelligent people that do the best with the tools provided them. However, they are often times not given all the proper tools or guidance. Instead, they are just given stringent metrics to meet.
Minimizing octane giveaway is routinely one of the top 2 gasoline blending metrics that refineries focus on. Depending on the location of the refinery and the complexity, this can either be a hard task to accommodate, or a very hard to task to accommodate. This challenge leads many gasoline blenders to pursue different pathways to meet the objective.
Most people believe that gasoline blenders are the ones who are responsible for octane giveaway. WRONG! If your refinery is currently operating under this guidance, then you are likely pissing money down the drain.
Gasoline blenders are the ones who develop and execute blend plans from the blend components made available by the refinery. They can no better control octane giveaway than a wide receiver controlling quarterback passing accuracy. Gasoline blenders surely have the ability to make a blend worse, but they can only make a blend as good as the components provided.
So let’s cover some common mistakes that refineries make when trying to minimize octane giveaway.
1. Setting a Constant Reformer Severity Target
Reformer severity is normally used to manage refinery hydrogen balances as well as refinery octane balances. As hydrogen and octane balance are highly dynamic constraints that depend on multiple variables, setting a constant reformer severity target is normally a sub-optimal practice.
Refinery optimization planners and gasoline blenders should work together to understand their constraints.
Is high reformer severity required all the time, or just
from time to time?
Is high octane reformate required in all of the gasoline
blends, or just premium blends?
Understanding these constraints can help determine how to set reformer severity. Often times, batch operating reformer severity may be the right solution to meet gasoline pool requirements while maximizing refinery yields and catalyst utilization.
2. Blending Low Octane Components to Reduce Giveaway
Using low octane blendstock (i.e. treated straight run naphtha) to reduce excess gasoline pool octane is equivalent to spraying Febreze in a Porta Potty. You may cover the stink, but the rotten turd still exists.
Before a blender uses high a volume of low octane blendstock, they should ask themselves: Why do I have so much octane length in my blend pool?
If the answer is not hydrogen balance, then there’s a likely chance that improvements can be made. Options include:
|
You may have made a double-take on the last bullet above. Just allowing the octane giveaway to remain? Yes, octane giveaway can make sense in markets where jet prices are higher than that of gasoline. If the other options remain non-viable, blenders should avoid producing more naphtha at the expense of jet just to reduce octane giveaway.
3. Segregating the Wrong Blend Components in Tankage
Every refiner will say that they do not have enough tankage. Every refinery blender will say this even louder. However, it is not common for refiners to take a step back and ask themselves if they have existing tanks utilized in the proper service.
If gasoline blend components share common tankage, understand the drivers behind why the pairings were chosen. A decade ago, these pairings may have made sense when blend specifications were not as complex, but do the pairings make sense today? People often paired components based on octane ratings, but today other specifications such as benzene and sulfur need to be considered as well.
For refineries that have dedicated rundown tanks for every blend component stream, they need not worry about this problem. For refineries that combine multiple blend components into one tank, this may be an opportunity to improve refinery octane balances.
While we are talking about tankage, tank size logistics may also play a factor in how to blend components are utilized. Depending on component production rates or finished product lift schedules, changing tank services to manage logistic constraints can often times improve blend planning and execution.
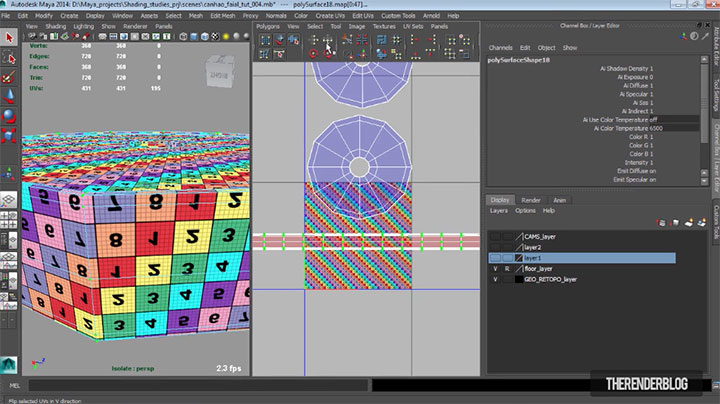

Engineers often spend too much time optimizing unit yields without understanding how poor logistics can negate all the front end efforts!
As with every single refinery constraint that we can focus on, minimizing gasoline blend octane giveaway relies on a combination of factors. Refiners who fall into the trap of relying on their gasoline blender to manage performance are just plain foolish.
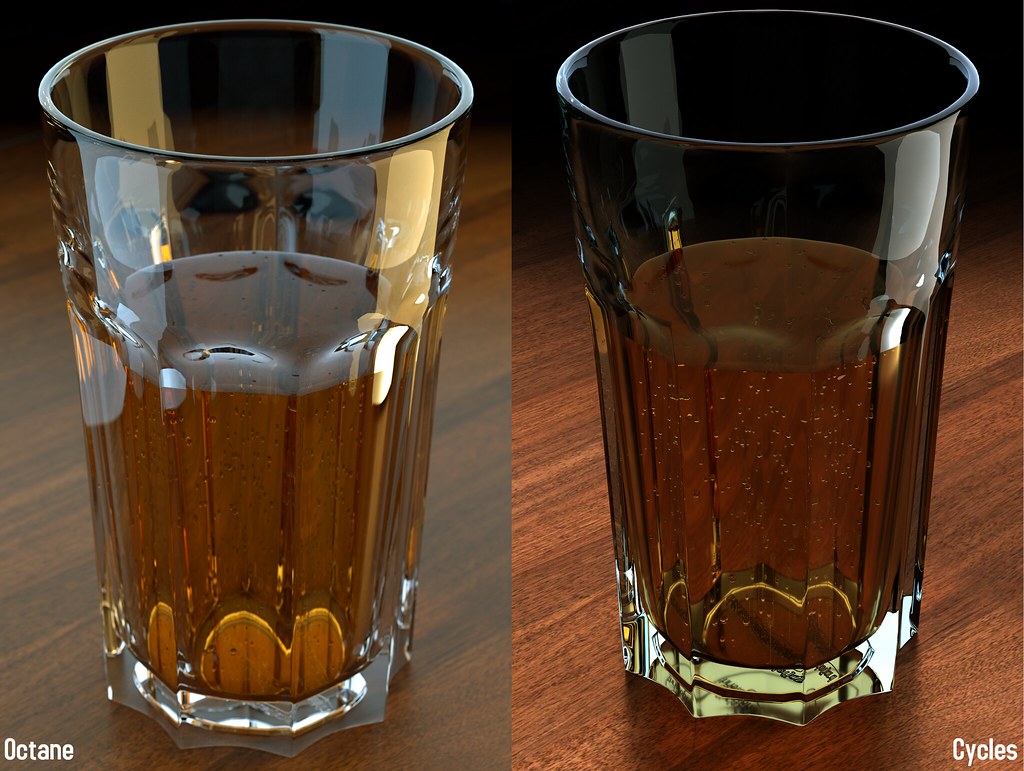
Great performance relies on coordination between numerous planning, engineering, and operations resources, and organizations need to ensure that all functions are properly supported. We all know that human beings will constantly endeavor to meet metrics. The real question is if the solutions to the metrics are the correct ones.
Octane Blender Free
Next time when you review your refinery’s gasoline octane metrics, think twice before believing that you are satisfied with your results.
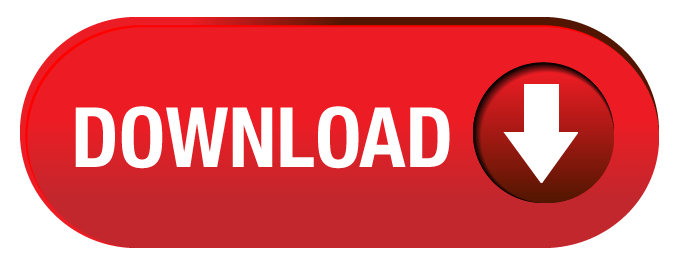